국내 연구진이 기존 프랑스산 에어덕트를 대체할 국산 경량화 에어덕트를 개발해 상용화를 앞두고 있다. 이는 국내 자동차 산업의 자립도를 높이고 차량 성능을 개선할 수 있는 기술적 성과로 주목받고 있다.
한국기계연구원(이하 기계연) 부산기계기술연구센터 배승훈 선임연구원 팀과 유진에스엠알시오토모티브테크노(유진SMRC A.T.), 에스에이치코리아 연구팀은 자동차 콕핏 모듈의 에어덕트 제조 기술을 획기적으로 개선했다. 개발된 제품은 성능평가에서 완성차 규격을 만족해 상용화를 준비 중이다.
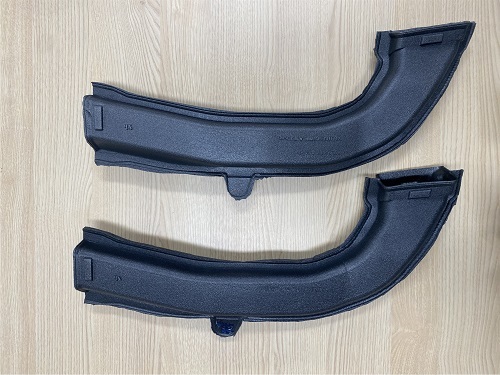
이번에 개발된 에어덕트는 기존 제품 대비 무게를 60% 줄였으며, 기밀성과 소음 저감 성능, 그리고 안전성 면에서 크게 향상된 점이 특징이다. 특히, 기존의 고밀도 폴리에틸렌(HDPE) 소재가 아닌 폴리에틸렌(PE) 발포 폼 시트를 적용해 단열 성능을 높였고, 소음 저감 효과를 극대화해 차량 연비와 승차감을 동시에 개선했다.
배승훈 선임연구원은 “기존 에어덕트는 단열 성능이 부족하고 조립이 불편해 차량 연비 저하 및 승차감에 부정적인 영향을 미쳤다”며 “새로 개발된 제품은 이러한 단점을 해결함으로써 다양한 차종에 적용 가능할 것”이라고 설명했다.
에어덕트는 진공 성형 및 핫나이프 공정이라는 새로운 제조 방식을 채택했다. 이 공정은 기존 블로우 성형보다 불량률을 낮추고, 복잡한 형상을 정밀하게 구현할 수 있어 생산성을 크게 높일 수 있다. 또한 PE 발포 폼 소재의 예열 및 상하 진공 금형 석션 방식으로 형상을 구현하고, 핫나이프 공정을 통해 가장자리를 정밀하게 절단하는 후처리 과정이 포함되어 있어 기존의 공정보다 효율적이다.
유진SMRC A.T.의 임성빈 연구소장은 “이번 개발로 품질, 원가, 경량화 측면에서 모두 우수한 부품을 생산할 수 있었다”며 “국내뿐 아니라 해외 시장에서도 경쟁력을 강화할 계획”이라고 밝혔다.
이번 연구는 산업통상자원부와 한국산업기술기획평가원의 ‘자동차산업 기술개발(그린카)’ 과제 지원을 받아 진행됐으며, 향후 제품 양산화를 통해 국내외 자동차 제조사에 공급될 예정이다.
이 기술의 상용화가 이루어지면, 국내 자동차 부품 산업의 자립도를 높이고, 완성차 업체의 수입 대체 효과를 기대할 수 있을 뿐만 아니라, 자동차의 연비 개선과 안전성 확보에도 크게 기여할 것으로 전망된다.
헬로티 임근난 기자 |