산업 제조 영역에서 디지털 트윈 기술은 빅데이터를 기반으로 현실을 반영하는 가상 모델을 생성하며, 이는 제조 설비의 설계부터 운영까지 전 과정을 가상화하여 효율성을 높이는데 기여한다. 반면, 메타버스는 사회적 활동을 가능하게 하는 가상세계를 제공하며, 이 두 기술은 각각 다른 출발점을 가지고 있지만, 산업 분야에서는 이들의 장점을 접목하여 지속 가능한 발전을 추구한다.
지멘스는 이러한 변화를 주도하기 위해 ‘지멘스 엑셀러레이터(Siemens Xcelerator)’를 통해 파트너와 협력하며 맞춤형 솔루션 개발을 위해 노력하고 있다. 또한 기존 및 신규 공장에 대해 각기 다른 접근 방식을 제안하며, 중소규모 공장도 클라우드 기반 서비스를 통해 접근성을 높이고 자원 효율성을 개선할 수 있다고 제시한다.
지멘스가 제시하는 산업 생산을 위한 혁신 가속화 방안은 무엇인지, ‘2024 스마트 제조 대전망 온라인 컨퍼런스’에서 한국지멘스의 김태호 이사가 발표한 내용을 정리했다.
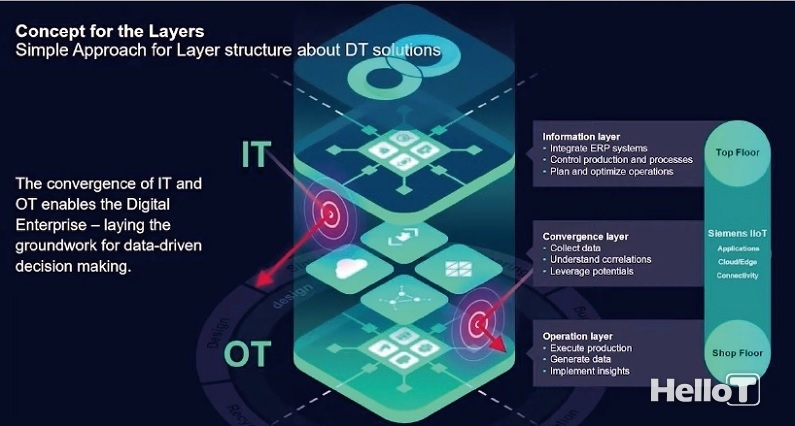
산업 제조 영역에서의 디지털 트윈 기술은 제조 설비에서 도출된 빅데이터를 가상세계에 도입한 후 테스트를 거쳐 그 결과를 현실에 반영하는 개념이다. 지금은 기존의 단순한 디지털 트윈 활용 흐름과 달리 가상의 개념이 더욱 확장된 방식을 차용하기 위해 기술이 개발되고 있다.
같은 ‘가상’의 요소를 지닌 디지털 트윈과 메타버스는 지향점은 같지만 출발점은 다르다. 디지털 트윈은 자율주행과 같이 데이터를 가지고 전체적인 현실을 정확하게 반영하는 리소스가 필요하다. 반면 메타버스는 가상세계 안에서 사회적 활동을 할 수 있는 일종의 흥미 위주의 그래픽 리소스, 즉 참여형 솔루션이라는 점이 디지털 트윈과 다른 점이다. 산업은 이 두 기술의 장점을 접목한다는 관점에서 지속가능성 확장을 주목하고 있다.
OT와 IT의 결합, 기반은 ‘빅데이터’
글로벌 스마트 엔지니어링 기술 기업 지멘스는 제조 혁신 가속화를 목표로, 빅데이터를 관리하고 활용해 현실에서 얼마나 지속 가능한 수익 창출할 수 있을지, 나아가 이를 활용해 생활상 편의를 지속할 수 있을지 질문을 던진다. 여기에 기반이 되는 기술이 개방형 디지털 비즈니스 플랫폼 ‘지멘스 엑셀러레이터(Siemens Xcelerator)’다.
해당 기술은 빅데이터를 활용해 현실에 반영할 수 있는 요소를 제공하기 위해서는 일반 산업 분야에서 기존에 활용했던 기술만으로는 부족한 것이 현실이다. 이에 지멘스는 파트너들과 생태계를 구축해 각자의 장점을 융합한 맞춤형 솔루션을 제시하겠다는 비전을 설정했다.
가령 그래픽·예지보전 등 각 분야에 강점을 보유한 파트너의 역량과 자사 역량을 접목해 한 단계 진보된 솔루션을 주는 콘셉트다. 이 과정에서 빅데이터를 총체적으로 관리하기 위한 완성된 클라우드 및 인공지능(AI) 솔루션을 도출하는 것이 최종 목표다.여기서 핵심은 데이터를 어떻게 활용하느냐다.
그렇다면 제조 분야에서의 데이터는 무엇을 의미할까? 일반 생산 공장에서 한 달에 확보되는 데이터량은 약 2200테라바이트(TB)로 알려져 있다. 이는 스트리밍 영화 약 50만 편 정도 되는 분량이다. 우리는 실생활에서 이정도의 데이터를 무리 없이 다룬다. 하지만 산업 영역에서는 얘기가 다르다. 이미 자동화나 무인화에 대한 기술은 이미 준비가 됐기 때문에 데이터를 관리하고, 활용하는 측면에서의 디지털 전환이 필요한 시점이다. 쉽게 말해 생산 라인에서 기존에 각각 따로 관리됐던 공정을 빅데이터라는 통합된 데이터 접근 방식을 통해 모든 것을 동시에 관리하는 것이 필요하다.기존에는 OT 영역에서 활용했던 데이터를 모두 OT와 IT가 통합된 솔루션으로 검증을 할 수 있는 시대가 도래했다. 이것이 바로 디지털 트윈을 통한 시뮬레이션 검증이다.
‘가상세계’가 가진 힘
서두에도 언급했듯 디지털 트윈은 빅데이터를 매니징하는 기술이다. 제조 설비 설계 단계에서는 이 기술을 활용해 가상현실에서 공정 라인을 설계한 후 IT에서 물성에 대한 시뮬레이션 결과를 OT 레벨의 시뮬레이션에 반영한다. 이후 반영된 데이터를 가지고 PLC를 구축하고, 기본 템플릿 데이터가 도출된다. 대부분 설계 도면을 기반으로 구축되기 때문에 실제 공장과 함께 가상현실의 또 다른 공장이 연결된다. 이 가상 공장은 데이터를 지속 생산해내는 임무를 가진다. 이렇게 만들어진 데이터는 실제 공장 운영에 활용되고, 가상 공장은 데이터 최적화를 돕는다. 그리고 실제 생산 라인에 반영한다. 이 과정을 거치면서 실제 공장과 가상 공장은 서로 동기화된다. 결국 디지털 트윈은 완성형 스마트 팩토리의 탄생에 기여하는 기술이다.
이 과정에서 데이터 간 연결이 중요한 포인트다. 기존에는 센서나 필드 레벨의 컨트롤 데이터가 PLC 데이터에서 중앙 집중 제어 방식의 SCADA 솔루션에 연결되고, 계층별로 구분됐다. 데이터가 통합적으로 관리되면 클라우드를 기반으로 현장 장비와 데이터가 연결된다. 지멘스는 현장 장비의 연결 또한 중요하다고 말한다. 이를 위해 특정 게이트웨이 솔루션을 제안한다. 해당 기술을 활용하면 작업자가 일일이 장비를 모니터링하지 않아도 통합적인 관리가 가능하다. 그래서 연결성이 중요하고, 이와 관련해 클라우드에서 리소스를 관리하는 등 방식으로 데이터를 관리하는 것이다.
디지털 트윈를 통한 데이터 관리의 최대 장점은 매핑된 설비 및 오브젝트를 모두 그래픽 리소스로 가져온다는 것, 즉 모든 공정을 렌더링하는 것이다. 쉽게 말해 공정 내 볼트 하나까지 전부 다 오브젝트화 한다. 그렇게 되면 각각의 객체가 하나의 물체처럼 인식된다. 기존에는 이런 일련의 과정을 사람이 오브젝트별로 리소스화한 다음, AI 클라우드 베이스의 솔루션에 올려 체크했다. 디지털 트윈을 활용하면 자동으로 생성된다. 궁극적으로 데이터를 기반으로 의사결정을 수행하는 ‘데이터 드리븐(Data Driven)’이 가장 중요한 요소라고 보면 된다.
‘데이터 드리븐’의 선결 과제는?
지멘스는 기존 공장(Brown Field)과 신규 공장(Green Field)을 구분해 솔루션을 도입하는 것을 추천한다. 기존 공장은 연결성을 핵심으로 솔루션을 녹이고, 신규 공장은 데이터 검증을 중점으로 솔루션을 가져가는 방향성이다. 특히 신규 공장은 데이터 검증에 많은 자원이 소모되기 때문에 해당 관점이 요구된다.
이미 데이터 드리븐이 완료된 공장은 AI 활용이 용이하고, 완성형 디지털 트윈이 가능하다. 이는 대규모 공장에만 국한된 개념으로 알려졌다. 중소규모 공장은 이를 위한 시행착오를 겪는데, 지멘스는 비교적 진입장벽이 낮은 클라우드 기반 서비스를 통해 해결 가능하다고 강조한다. 리소스를 관리하는 데 소모되는 자원보다 클라우드 서비스를 활용하는 것이 자원 효율성 측면에서 유리하다는 것이 그 이유다.
오토메이션월드 최재규 기자 |