디지털 트윈의 사전적 의미는 스마트 산업 전반에 걸쳐 통상적으로 사용되고 있지만 제조 산업에 적용한 사례는 조금은 다른 접근 방법이 필요하다.
제조 산업에서의 디지털 트윈의 역할은 크게 두 가지로 분류해 볼 수 있다. 첫 번째는 현장과의 실시간 데이터 연동을 통한 모니터링의 역할, 두 번째는 미래 예측 및 조기 대처를 통해 제조 생산·운영을 최적화하는 역할이다.
두 번째 역할은 다시 목적에 따라, 주기적인 시뮬레이션을 이용하여 미래 예측 및 조기 대처를 통한 제조 생산·운영의 최적화, 이상 상황에 대한 빅데이터를 수집하여 다양한 AI로직을 적용한 생산·운영의 최적화로 분류할 수 있다.
생산·운영의 최적화를 달성하기 위해 많은 기업들은 하나의 통합된 환경이 아닌 각각 다른 솔루션을 활용한 것이 대부분이며, 실제 현장과의 정합성이 다른 결과를 초래하기 때문에 진정한 의미의 최적화를 달성하기 어려운 실정이다.
CARLO는 제조 생산·운영의 최적화를 달성하기 위해 통합된 환경에서 디지털 트윈을 쉽게 구축할 수 있는 PINOKIO 솔루션을 소개하고자 한다.
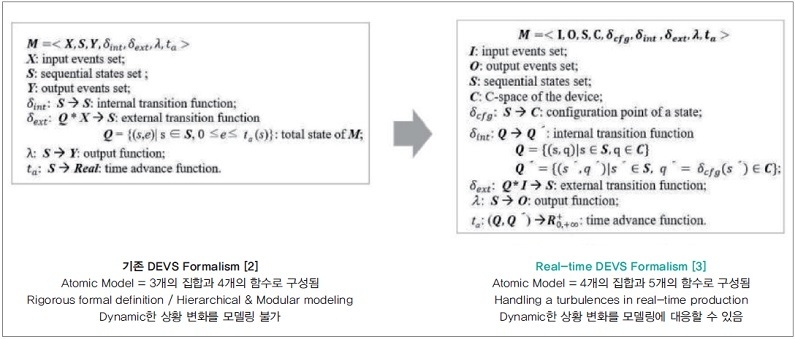
대용량 데이터 처리 및 실시간 모니터링 시스템 : PINOKIO
실시간 모니터링의 목적은 현장 상황을 보다 신속·정확하게 파악하고 선제적인 대응을 위한 것이다. 디지털 트윈 전문기업들은 실시간 모니터링이 가능한 솔루션들을 시장에 선보였다. 대부분은 로봇의 기하학적인 분석, 엔진의 역학 분석 등 단일 부품 및 설비에 초점이 맞춰져 있지만, 대규모의 제조 생산 라인에 적용된 사례는 드문 것이 사실이다.
몇 가지 사례는 실제로 제조 현장에 있는 듯한 현실감 있는 3D 애니메이션을 제공한다. 하지만 생산·운영의 최적화를 위해서는 현장에서 발생하는 대용량의 데이터를 수집하여 실시간 연동 모니터링이 구현되어야 한다.
PINOKIO는 MES와 센서에서 발생하는 대용량 데이터를 실시간으로 처리하여 현장의 모습을 가시화한다. 또한, 처리된 데이터는 제조 현황과 운영 단계에서의 예측 시뮬레이션에 사용되며 그 결과가 대시보드 형태로 제공된다.
시뮬레이션 가속 성능
시뮬레이션에서는 이벤트의 개수가 속도의 큰 영향을 미치는 요소이다. PINOKIO는 이벤트의 개수를 최적화하여 최소한의 이벤트로 시뮬레이션이 가능하도록 기존의 상용 솔루션보다 성능을 개선했다. 또한, 솔루션에 포함된 알고리즘을 계산 속도의 이점을 가진 C, C++언어로 구현하여 기존 솔루션들에 비해 2만평 규모의 공장에서 약 70배의 향상된 성능을 검증했다.
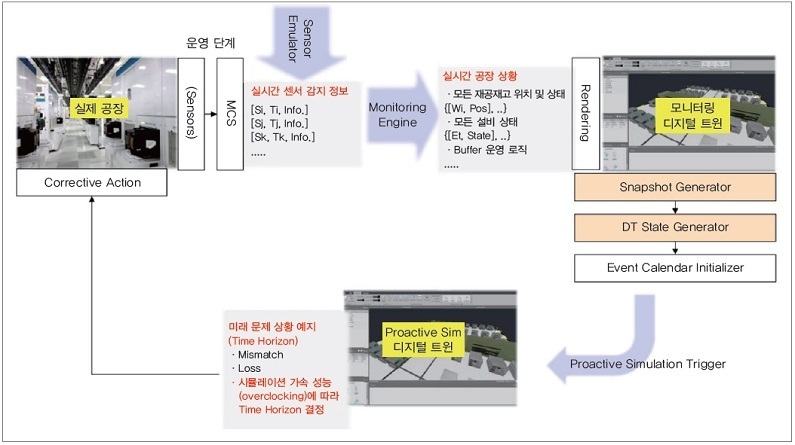
PINOKIO 작업 프로세스
PINOKIO는 모니터링 엔진을 통해 현장의 MES와 센서 데이터를 집계하고 현장과 동일한 물류의 흐름을 실시간 모니터링할 수 있다.
MES와 연동하여 수집한 데이터로 디지털 트윈 모델을 생성하여 물류 흐름을 가시화하고, 사용자가 설정한 시간 주기마다 미래를 예측하는 시뮬레이션(Proactive Simulation)을 백그라운드로 수행한다. 실시간 라인의 상황을 반영한 시뮬레이션은 제품의 공정 Tact Time보다 짧은 시간 안에 결과를 확인할 수 있다. PINOKIO는 제조 현장과 동일한 상황을 디지털 트윈화하고 계획 시점이 아닌 운영 시점에 시뮬레이션을 통해 보다 정확한 의사결정을 내릴 수 있도록 지원한다.
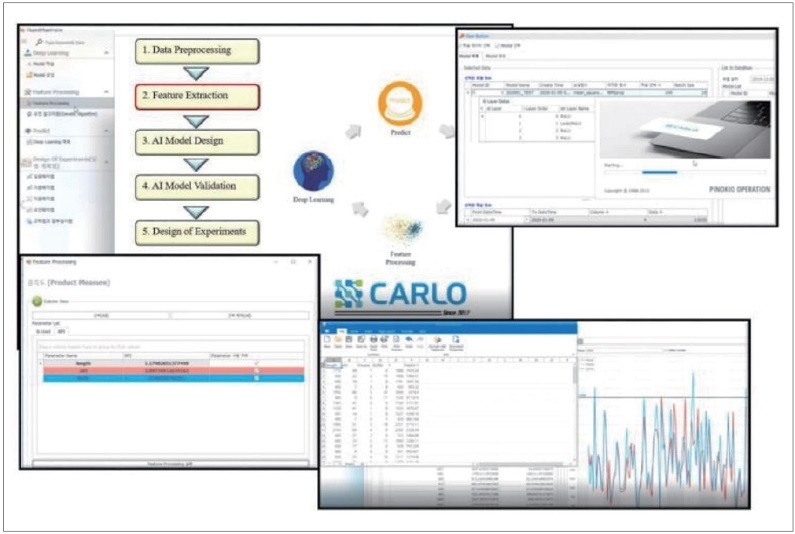
AI Platform CAP
AI를 이용한 솔루션을 만들기 위해서는 정상적인 상황뿐만 아니라 이상 상황에 대한 데이터를 필요로 한다. 하지만 제조 현장의 생산성을 저해할 수 있는 이상 상황을 모사하기 위해 공정 파라미터를 바꾸며 데이터를 획득하기 어렵다.
PINOKIO는 실시간으로 연동되어 있는 정합성 높은 가상의 환경에서 시뮬레이션을 통해 이상 상황에 대한 대용량의 데이터 획득이 가능하다. 이러한 특징은 AI로직을 개발하기 위해 필요한 데이터를 확보할 수 있다.
PINOKIO에서는 획득한 데이터를 통신을 이용하여 python, c, c++, c#, java 등 다양한 언어들과 연동할 수 있고 실시간으로 솔루션 내에서 AI 로직을 적용 및 검증할 수 있는 플랫폼을 제공한다.
PINOKIO 사례
‘L’사의 제조 라인에 PINOKIO 디지털 트윈 플랫폼을 구축하여 현장 작업자는 실시간 모니터링을 통해 현장을 파악하고 있으며, 예측 시뮬레이션의 결과를 통해 미래에 발생할 수 있는 생산 로스를 미리 대처하는데 사용하고 있다.
또한, 국내 가전업계 중 처음으로 세계경제포럼(WEF)이 발표한 ‘등대공장’에 선정되는 데에 기여하였다.
‘S’사의 반도체 라인에 PINOKIO 디지털 트윈 플랫폼을 구축하여 정합성이 약 98%를 달성하였고 기존 솔루션 대비 2만평 규모의 공장에서 약 70배의 향상된 가속 성능을 검증했다.
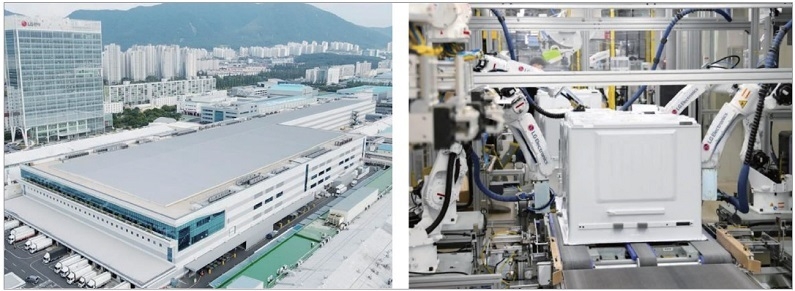
PINOKIO와 현장 인터페이스
대부분의 전문 솔루션은 현장과 다양한 인터페이스를 지원한다. 하지만 현장 데이터를 가공하여 시뮬레이션까지 사용하는데 어려움이 있다.
PINOKIO는 대용량 처리가 가능하고 실시간으로 시뮬레이션까지 가능하다. 이는 흔히 말하는 실시간 모니터링 시스템으로 사용 가능하다. 현장에 있는 PLC데이터가 MES에 전달되고, 그 데이터를 MES는 데이터베이스에 저장한다. 이를 PINOKIO®에서 외부 통신(IP)을 통해 데이터베이스에 접근하여 현장과 인터페이스가 된다. 이 과정에서 현장 데이터가 유실되거나 불필요한 데이터, 시간 순서가 맞지 않은 경우가 발생할 수 있다. PINOKIO는 현장 데이터를 정규화하여 실시간으로 현장과 연동한다.
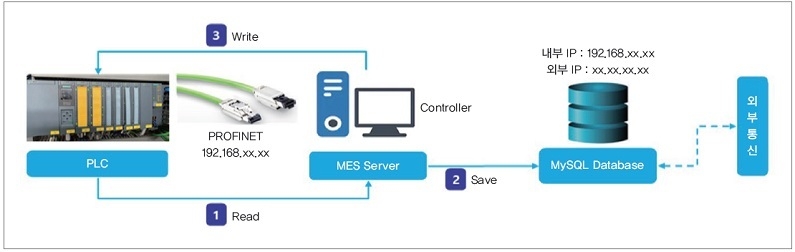
PINOKIO 적용 효과
PINOKIO는 실시간 모니터링을 통해 현장 상황을 파악하고 문제점을 예측하여 선제적인 대응을 가능하게 하여 생산·운영의 최적화를 달성할 수 있게 도와준다.
또한, 기존에 만들어 놓은 타사의 시뮬레이션 모델 및 레이아웃, 기준정보들은 일부 컨버팅이 가능하기 때문에 디지털 트윈을 구축하는데 시간과 비용을 절감할 수 있다. 사례에서 소개하였듯이 현장 작업자와 연구 인력을 하나의 통합된 환경으로 유기적인 플랫폼을 구축할 수 있다.
결론
현장 작업자의 개입과 같은 인간적 오류는 시스템이 예측할 수 없는 데이터를 발생시키기 때문에 계획 단계에서의 사전 분석 및 검증만으로는 시뮬레이션의 결과를 통해 의사결정을 내리는 것에는 한계점이 존재한다. PINOKIO는 현장 상황에 대한 신속·정확한 파악과 운영 단계에서의 미래를 예측하는 시뮬레이션의 통합은 보다 정합성이 높은 의사결정에 도움을 줄 수 있다. 또한, AI개발 플랫폼을 제공하여 다양한 스마트 제조 연구 인력들을 활용할 수 있다.
결과적으로, PINOKIO는 실시간 모니터링을 통해 현장 상황을 파악하고 문제점을 예측하여 선제적인 대응을 가능하게 하고, 더 나아가 생산·운영의 최적화를 달성하기 위해 통합된 환경의 디지털 트윈을 구축할 수 있는 솔루션을 제공한다.