조선업계는 업황의 개선에도 기술자의 리턴이 거의 없어 외국인 노동자로 채울 수밖에 없는 큰 어려움을 겪고 있다. 조선3사의 경우 이러한 인력난을 타개하기 위해 최근 무인자율운향, 스마트조선소를 추진하고 있다. 특히, 많은 용접 작업이 수행되는 공정 특성상 용접용 로봇 자동화 대한 필요성은 점점 부각되고 있다. 따라서 대조립, 중조립, 소조립 공정을 중심으로 용접로봇의 설치 및 운영에 대한 연구가 활발히 진행되고 있다. 조선 분야 제조혁신을 위한 최근 연구사례와 로봇 적용사례에 대해, 한국조선해양미래기술연구원 윤대규 전문위원이 제조혁신 세미나에서 발표한 내용을 정리했다.
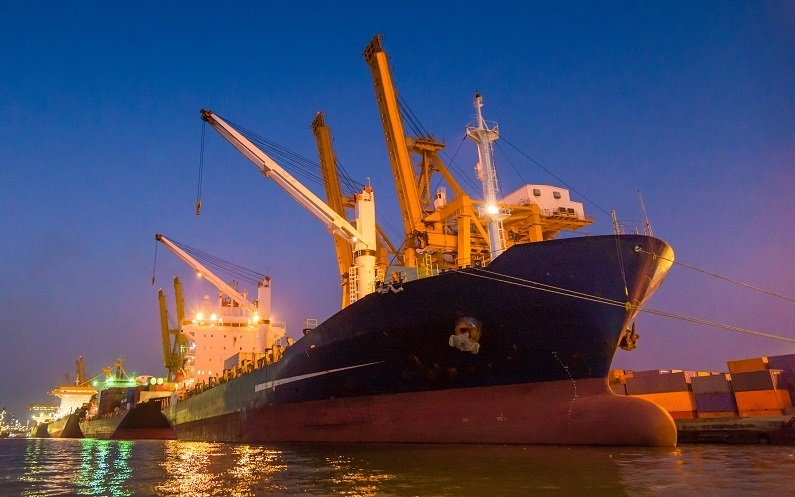
지금 조선산업은
우리나라 조선업계는 올해 수주 목표를 조기에 달성할 정도로 호황기이다. 발주 시장이 활기를 띠면서 액화천연가스(LNG) 운반선, 석유화학제품(PC) 운반선 등의 수주 선가도 역대 최고가로 계속 오름세에 있다.
9월말 기준 조선 빅3(한국조선해양·대우조선해양·삼성중공업)는 각사 연간 수주 목표의 80~120%를 달성 중이다. 현대중공업그룹의 조선 중간지주사인 한국조선해양은 2022년 연간 수주 목표 174억4000만 달러를 일찌감치 넘겼다. 한국조선해양은 LNG 추진 컨테이너선과 PC선 등 8척을 수주하면서 9월 현재까지 총 203억5000만 달러를 수주했다. 연간 목표를 116.6%로 초과 달성했다.
대우조선해양은 올해 LNG운반선 30척 등 총 86억 달러의 수주를 올려 올해 목표 89억 달러의 97%를 거의 채웠다. 삼성중공업도 LNG선 수주 물량을 포함해 올해 총 37척, 72억 달러의 오더북을 기록하며 연간 목표 88억 달러의 82%에 도달했다.
하지만 이러한 수주 호황에도 조선업계는 인력난에 고민이 깊어지고 있다. 한국조선해양플랜트협회에 따르면 사내 협력사를 포함한 국내 조선소 인력은 2014년 말 20만3441명에서 지난해 말 9만2687명으로 7년 사이 절반 가까이 감소했다. 조선업계는 업황의 개선에도 기술자의 리턴이 거의 없어 외국인 노동자로 채울 수밖에 없는 큰 어려움을 겪고 있다.
조선 3사는 이러한 인력난을 타개하기 위해 최근 무인자율운항, 스마트조선소를 추진하고 있다. 그런데 스마트조선소를 구축하기 위해서는 생산 공정의 자동화가 먼저 이뤄져야 한다.
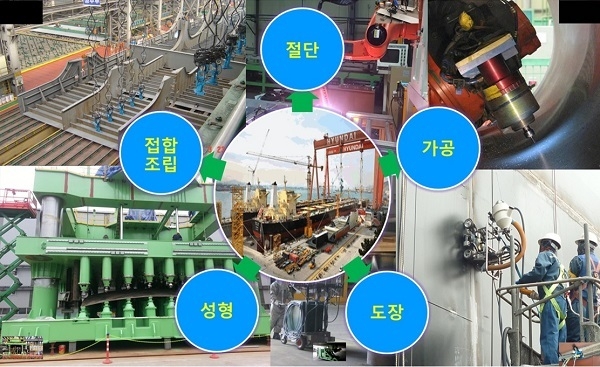
조선산업 공정과 자동화
선박 공정은 크게 ‘절단, 가공, 도장, 성형, 접합 조립’ 5가지로 분류할 수 있다. 현재 선박 건조는 용접기술의 비약적인 발전에 힘입어서 선체를 수십 개의 블록으로 분할하고, 도크 내 크레인을 이용해서 소조립, 중조립, 대조립 순으로 제작하는 블록 건조법이 주류를 이루고 있다. 또한, 강재절단과 소조립, 중조립, 대조립 공정에서는 자동화가 많이 진행되고 있지만, 선행 도장이나 의장에 있어서는 작업 특성상 복잡함과 어려움 때문에 자동화가 덜 된 편이다.
이런 부분들을 해결하기 위한 기술로는 어떤 게 있을까. 우선, 선체 내부를 구성하는 구조들을 보면 크기, 중량, 형상에 따라 아주 복잡하고 다양하게 존재한다. 특히, 블록의 형상에 따라 평블록과 곡블록으로 분류할 수 있는데, 평블록은 라인 시스템(Line System)화 되어 부재 취부작업의 자동화 장치, 용접작업의 자동화 장치 등이 설치되어 있으나 곡블럭은 전 공정에 걸쳐 대부분의 조립작업이 수작업에 의존하고 있다.
몇 가지 예를 살펴보겠다. 선체의 미들섹션부는 평블록으로 오픈 타입의 구조와 밀폐 타입의 구조로 되어 있다. 선박 생산의 가장 많은 부분을 차지하고 있는 이곳은 구조물 크기 대비 상대적으로 자동화가 용이해, 로봇 자동화를 활용하고 있다.
반면, 선체의 선수부와 선미부는 곡선이 상당히 많아 자동화 수준이 가장 낮다. 주로 곡면으로 이루어져 있기 때문에 곡선형 및 취부 작업의 정도 확보에 어려움이 있어 용접은 숙련자 기반의 수작업에 의존하고 있다.
선체 내부 의장재도 상당히 복잡한 형상을 가지고 있다. 파이프 류 용접이나 의장품 연결 작업 및 조립 등이 필요하기 때문에 이 또한 숙련자 기반의 수작업에 의존한다. 최근엔 용접자동화 장비가 많이 개발되면서 간이 자동화가 부분적으로 이루어지고 있다.
도크(Dock) 단계는 지상에서 블록의 연결 작업만 수행하는 공정이지만 블록끼리 이음작업의 환경은 매우 위험하고 협소하므로 생산성이 가장 낮은 공정이다. 작업 환경뿐만 아니고 연결 작업 및 용접 작업 그 자체도 선공정에서의 누적 편차, 골리앗 크레인에 의한 미세 조정 작업의 어려움, 대기온도에 의한 제품의 신축현상, 용접 진행 과정에서의 수축 등의 문제점이 다발하여 연결부의 적정 갭(Gap) 유지를 위한 재작업이 매우 많은 실정이다. 따라서 최근엔 시뮬레이션 해석 기법들을 적용해서 건조에서의 조립 작업을 할 때 어긋나는 부분들을 최소화할 수 있는 기술들이 개발되고 있다.
제작 전체 공정에 관여하는 도장 공정은 작업 환경이 가장 열악하고 자동화를 위한 난이도가 매우 높다. 설령 자동화가 구현되더라도 생산성 개선의 확보가 어려운 특성을 가지고 있다. 때문에 여전히 숙련자 기반의 수작업에 의존한다. 그러나 일부에서는 사람들이 크레인을 타고 작업하는 반자동화나 바닥에 장비를 활용해서 자동 코팅처리 하는 부분적인 도장 자동화가 진행되고 있다.
조선산업 자동화 필요 기술
자동화는 적용되는 범위와 장비의 특성에 따라 완전 자동화, 부분 자동화, 간이 자동화 3가지로 나눠볼 수 있다. 일반적으로 자동화의 최종적인 목표는 전체 공정을 자동화하는 완전 자동화이지만, 조선산업의 특성상 단위공정을 기능형 장비 또는 비숙련자와 같이 협업 환경을 구축해서 할 수 있는 부분 자동화가 중간 단계에 있을 수 있고, 단위 공정의 부분적 기계화 장비를 통해서 진행하는 간이 자동화가 있을 것이다.
앞서 언급했듯이 소조립, 중조립, 대조립 공정에서는 자동화가 가능한 부재들이 많이 있기 때문에 완전 자동화를 위한 공장 구축 사례가 많이 이루어지고 있지만, 내업이나 건조, 의장, 도장 작업과 같은 공정은 현실적으로 완전 자동화가 어렵기 때문에 간이 자동화 또는 부분 자동화를 목표로 삼고 있다. 그래서 그에 맞는 장비들이 개발되고 있다.
그렇다면 조선산업의 로봇 응용 기술은 일반 산업체와 어떤 차별화된 기술이 요구될까. 조선산업에서 요구되는 기술을 살펴보면, 로봇 적용성 검토와 최적 사양 선정을 위한 사전 시뮬레이션, 로봇 부가축 및 포지셔너, 부재 인식을 위한 센서 기반 적용 기술, 그리고 오프라인 프로그래밍 시스템 및 로봇 모니터링 시스템 등이 필요하다. 또한, 작업자가 들고 들어가야 하거나 협소 부위 투입을 위해서는 작고 가벼운 로봇이 필요하다. 사내 자동화 목적에 맞는 산업용 로봇이 존재할 경우 이를 활용하여 생산 자동화에 적용하고 있지만, 사내 자동화 목적에 맞는 로봇이 존재하지 않을 경우엔 특수 로봇을 자체 개발하여 적용한다.
예를 들어, 최근 3kg의 페이로드를 처리할 수 있는 협동로봇이 출시됐는데, 자체 중량은 11kg에 불과할 정도로 소형화, 경량화됐다. 자체 로봇 개발 후 적용된 사례도 있다. 현대중공업은 가반중량 5kg, 자체 중량 15.6kg에 불과해 작업자가 직접 들고 다닐 수 있으며 사람이 작업하기 어려운 협소 간 공간에서도 다양한 작업이 가능한 ‘용접용 포터블 소형 로봇’을 개발하여 선박 건조 생산현장에 적용하고 있다.
또한, 생산라인 자동화의 영역 확장을 위해서 비전 센서를 이용한 위치 인식과 보정 기술이 반드시 필요한 기반 기술로 자리매김을 하고 있다. 인공지능(AI) 기능을 탑재한 비전 센서는 소조립 용접 자동화, 곡 블록 용접 자동화 로봇 및 작업 위치 기반의 자동화 관련 모든 분야에서 공통적으로 적용이 가능하며, 특히 일반 정형화된 지그가 아닌 부재를 임의대로 놓고 작업을 해야 하는 공정 특성상 비전 인식과 보정 기술은 매우 중요하다고 볼 수 있다.
실시간 seam 추적에 기반한 자동 조향 기능을 가진 자율주행형 용접장비도 상용화가 진행되고 있다. 사람이 큰 부재의 용접을 할 경우에 지그와 같은 부대 장치가 많이 필요하게 되는데, 주행 장치를 자동화하게 될 경우 부가 설비가 필요치 않게 된다.
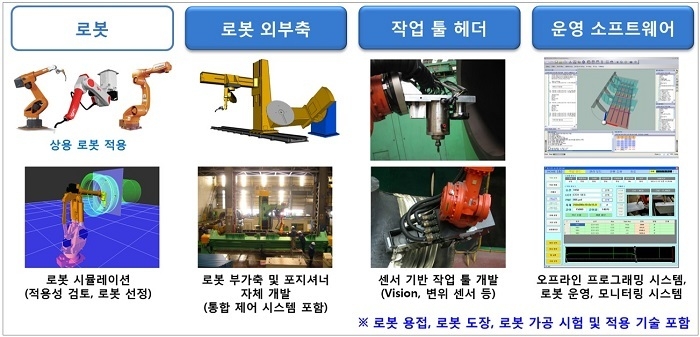
조선산업 용접자동화
많은 용접 작업이 수행되는 조선소에서의 용접자동화에 대한 필요성은 점점 부각되고 있다. 최근 치열한 수주전과 인건비 상승, 그리고 인력 부족 등이 주요 원인이라 할 수 있다. 따라서 대조립, 중조립, 소조립 공정을 중심으로 용접로봇의 설치 및 운영에 대한 연구가 활발히 진행되고 있다.
그러나 조선산업의 특성상 로봇 적용이 어려워 용접자동화에 어려움을 겪고 있다. 그 이유를 보면 크게 5가지로 정리할 수 있다.
첫째, 주문자에 의한 다품종 소량생산을 하고 일반화된 규칙에 의한 생산라인을 흘리지 않는다. 둘째, 공작물의 형상이 복잡하고 대형 블록에서는 사람이 작업하기 어려운 좁은 공간이 많다. 셋째, 조선용 부재는 대형의 중량물인 관계로 고정위치에서 작업을 해야 하므로 로봇 설비의 이동성이 문제된다. 넷째, 부재가 다품종 소량이므로 프로그래밍 시간이 많이 소요되며, 또한 부재의 크기가 대형이므로 로봇 작업 범위에 한계성이 있다. 다섯째, 공작 오차를 내포하고 있다. 즉, 비틀림과 변형이 존재하고 그루브 선 및 형상에 오차가 발생할 수 있다.
그렇다 보니 가장 많이 팔리는 산업용 로봇이 매년 수십만 대가 적용되고 있으나, 조선업에는 겨우 누적 수백여 대만 적용되고 있는 실정이다.
용접용 로봇 자동화에는 소조립용 로봇, 대조립용 로봇, 파이프 용접용 로봇 등이 있다. 이들은 공정별 특성에 따라 대응 형태가 달라진다.
먼저, 소조립 작업은 평판에 Plate Bar나 Angle과 같은 단순 형태의 골재를 부착하는 1차 공정으로 전형적인 소량 다품종이며 다양하고 복잡하다. 작업물의 크기는 약 5~10톤 정도이며, 용접 부위는 대부분 Fillet Joint이다. 중조립 작업은 소조립된 부재를 일체화하는 2차 조립 공정으로, 소조보다 단순하다. 이처럼 소조립과 중조립은 부재가 단순하고 작지만 넓은 곳에 펼쳐져서 작업을 하기 때문에 겐트리 형태의 로봇을 설치해서 사용한다.
조선에서의 대조립 작업은 소조립 공정에서 완성된 부재들을 조합하여 하나의 육면체로 만드는 공정이며, 최종 탑재 공정의 기본 단위의 블록을 만드는 공정이다. 주로 큰 부재를 좁은 영역에서 용접해야 하기 때문에 로봇을 포인트로 이동하기 위해서는 트롤리 혹은 크레인이 필요하다.
특히, 소조립용 용접자동화는 성공 사례를 찾아보기 어려울 정도로 어떤 자동화보다 어렵고, 복잡한 수준의 다양한 부재가 존재한다. 이러한 부재의 특성 때문에 로봇 교시를 위해서는 자동 프로그래밍 생성 기술인 OLP(Off-line Programming)를 사용해야 하는데, 여기에는 2가지 방식이 있다.
하나는 CAD(Computer-Aided-Design-Based) 기반 OLP이다. 이 방식은 부재를 용접하기 위한 용접서를 생성하기 위해 공작물의 완전한 기하학적 기능을 제공하지만 공작물과 CAD 모델 간의 편차는 보정할 수 없다.
다른 하나는 비전 기반 OLP이다. 이 방식은 이미지의 수많은 라인에서 이상적으로 선택되지만, 복잡한 구조의 공작물에 대해서는 용접 효율성이 떨어진다.
최근 연구 사례를 보면, 이 두 방식을 따로따로 사용하는 것이 아니라 CAD 기반 오프라인 접근 방식과 비전 기반 오프라인 접근 방식을 체계적으로 결합한 새로운 오프라인 프로그래밍 방식이 대세를 이루고 있다. 바로 하이브리드 OLP이다. 이 방식은 두 기법을 융합함으로써 산출된 편차 검출 결과를 이용하여 용접 경로를 보정한다. 따라서 정확도와 효율성을 동시에 높일 수 있다.
향후 과제
지금의 조선소는 대부분 70년대 혹은 80년대에 지어진 공장으로, 여기에 새로운 자동화 시스템을 넣어서 활용하려다 보니 기존 공장 레이아웃과 충돌로 어려움을 겪고 있다. 따라서 전 공정에 대한 고속화·기계화 도입 및 설비의 효율적 활용을 위한 공장 전체 레이아웃의 종합적 검토와 일관성 있는 생산라인의 구축이 함께 수반되어야 할 것이다.
공장자동화 또는 용접자동화를 위해서는 협력업체와의 긴밀한 협업도 중요하다. 이를 위해서는 무엇보다 역량 있는 SI업체가 많이 육성될 수 있도록 정부 차원의 지원과 방안이 마련되어야 할 것이다.
헬로티 임근난 기자 |