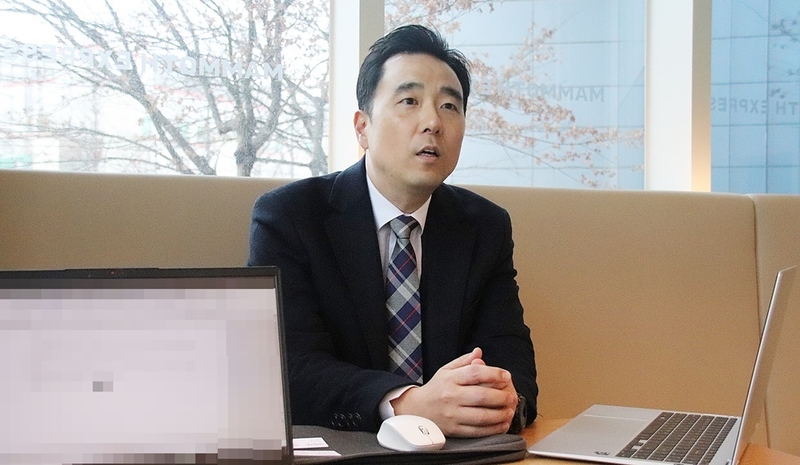
물체를 이어붙이는 과정에서 필요한 것이 뭘까? 접착 성분이 합유된 화학제를 생각할 것이다. 그렇다면 같은 맥락에서 금속 혹은 강철끼리 접합할 때 필요한 공정은 뭐라고 생각하는가. 통상적으로 용접을 떠올린다.
용접 공정은 높은 온도를 통해 접합 대상물을 한데 융합하는 작업으로, 주로 대상물 및 추가 소재를 녹인 후 굳기 전 압력을 가해 붙이는 과정으로 이해하면 된다. 용접은 각종 산업에서 활발하게 활용되고 있지만, 고열 및 섬광으로 인한 상해 및 화재, 고중량 대상물과의 충돌 사고, 용접 시 발생하는 유해가스(흄) 중독 및 폭발 이슈, 산소 부족에 의한 질식 위험 등 안전사고에 상시 노출된다는 단점이 있다.
여기에 작업자 역량에 의존하는 용접 공정 특성상 최근 도래한 글로벌 인력난에도 자유로운 수 없다. 이에 관련 업계에서는 용접의 치명적인 단점을 보완하는 새로운 공법의 접합기술을 속속 내놓고 있다. 레이저·전자빔 등 새로운 용접 공법, 타전 공구, 산업용 용접 로봇 및 용접 협동로봇, 주물 접착제 등이 이에 해당한다.
독일 기계 접합기술 및 장비 업체 톡스프레스테크닉(이하 톡스)은 독일의 규격시험인증 DIN 8593을 기반으로 한 접합 원천기술 ‘클린칭(Clinching)’을 보유했다. 해당 기술은 쉽게 말해 기계적 압력으로 대상물을 상호체결되는 구조로 성형해 접합하는 공정이다. 열, 가스 등을 이용하지 않아 안전사고에 대한 위험이 적고, 기계의 힘을 이용하기 때문에 생산성 및 효율성 제고의 강점도 갖췄다.
김기홍 톡스프레스테크닉 책임은 “클린칭 기술은 전 세계적으로 희소한 차별화 접합기술”이라며 “톡스는 이 원천기술과 더불어 함께 활용되는 제품과 설비에 대한 역량도 보유한 접합 분야 턴키 솔루션 업체”라고 강조했다.
실제로 톡스는 턴키 솔루션 업체의 입지를 공고히 하기 위해 설비에 이식되는 유공압 실린더, 서보 프레스 및 툴링과 이를 제어하기 위한 컨트롤러, HMI 등 핵심 요소를 제공한다.
높은 기술적 수준 요구하는 기계적 접합기술 '클린칭'
클린칭은 볼트·너트 등 엘리먼트 기반 방식과 별도의 엘리먼트를 요구하지 않는 방식으로 세분화됐다. 보통 두 개의 소재를 누르는데 하단 위치한 소재에는 원형 돌출부가 생성되고, 상단의 소재가 그곳으로 파고들어 접합하게 된다.
소재, 두께 등 대상물의 요소에 따라 적합한 툴을 활용해야 하기 때문에 특화된 기술력을 요구한다. 톡스는 2Ø(원주율 이하 Ø)부터 16Ø에 이르기까지 다양한 형태의 전용 툴을 구성했다. 하나의 Ø 내에서도 수많은 경우의 수가 도출되기 때문에 최적화된 기술 역량이 필요하다.
톡스의 클린칭은 두께 0.2~30mm, 각종 형태의 강철 및 비철, 도금·도장을 포함한 모든 조도 수준 등 조건을 수용해 소재를 접합한다.
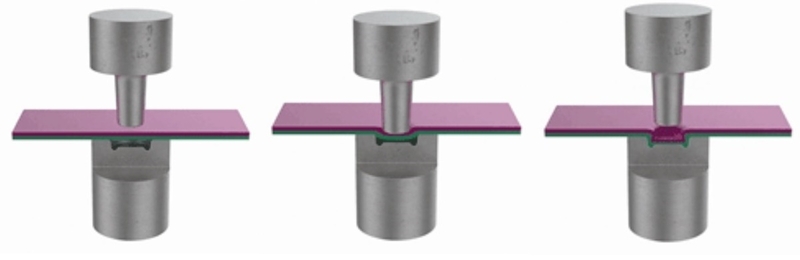
김기홍 책임은 용접 방식 대비 친환경적면서도 경제적인 클린칭의 특성을 내세웠다. 그는 “이 기술은 생산공정의 전수검사 과정에서 용접 방식과 대비된다”며 “프로세스 모니터링이 가능한 만큼 정밀한 작업이 가능해 제약이 많은 용접과 비교하면 품질 측면에서 앞선다”라고 역설했다.
클린칭은 이 과정에서 힘 센서, 스트로크 센서 등과 연동해 자동화 공정도 구현한다. 이에 따라 작업자의 역량에 의존하지 않으면서도 결과물의 미세한 결함까지 예방한다. 여기에 구리, 알루미늄 등 소재도 다룰 수 있어 전도체 공정에서도 활약한다.
톡스는 설비 구축부터 연구개발(R&D), 생산까지 요소를 고려하는 장비 업체에 해당 기술을 제시한다.
‘가전부터 이차전지까지’ 클린칭의 활약 무대
톡스는 클린칭 기술을 통해 자동차, 이차전지 등 차세대 산업과 가전기기 생산 공정에서 활동하고 있다. 김기홍 책임은 특히 검증 과정이 까다롭기로 유명한 이차전지 분야에서 독보적인 입지를 구축하고 있다는 점을 강조했다.
김 책임은 “클린칭은 용접이 어려운 알루미늄 소재와 서로 다른 소재의 강점을 드러낸다. 자동차·이차전지 등 산업과 알루미늄 등 경량화 소재를 채택하는 산업에서 주로 활약하고 있다. 용접 대비 결합 강도가 높고, 열을 가하지 않으니 열과 충격에 약한 알루미늄의 변형도 발생시키지 않는다. 힘과 변형량의 추적을 통한 비파괴 품질검사 또한 수행한다.”고 언급했다.
자동차 차체는 강성을 위한 접합, 이차전지에서는 배터리 셀과 모듈을 연결하는 ‘버스바(Busbar)’ 공정 등에 도입됐다. 지난 2월 경기 화성시 동탄 소재 톡스 센터에서 이차전지 고객사를 초청해 공정 시연 과정을 연출하기도 했다.
김기홍 책임은 “톡스는 자동차와 이차전지 산업이 발달한 국가에 법인을 구축이 완료된 글로벌 회사로, 연구개발에 매진해 산업군을 확장하고, 산업 요구에 지속 발맞출 것”이라고 전했다.
헬로티 최재규 기자 |