자동차 산업이 100년에 한 번 있는 변혁으로서 자동차의 전동화·지능화에 대응하는 가운데, 닛산자동차에서는 세계 최초로 2010년에 전기자동차(Electric Vehicle: EV 또는 Battery EV, BEV) ‘닛산 리프’을 양산하기 시작했다. 그 후 많은 전기자동차가 BEV 시장에 진출해 경쟁력을 유지하기 위해 차량의 모델 체인지에 맞춰 전동 파워트레인의 성능을 향상시키고 또한 그 제어도 개량·발전시켜 왔다. 2016년에는 BEV의 전동 파워트레인과 구동계를 공용하는 100% 모터 구동 e-POWER를 일본 시장의 ‘닛산 노트’용으로 선보였다.
e-POWER는 파워트레인 방식으로서 시리즈 하이브리드로 분류되는데, 다른 하이브리드 시스템과 차별화해 높은 가속 성능과 액셀 조작성을 BEV의 개발로 얻은 전동 파워트레인의 제어를 통해 실현하고 있다. 현재는 BEV를 비롯해 100% 모터 구동 차량이 많이 시장에 투입되고 있는데, 전동 파워트레인 제어의 관점에서 정리된 문헌은 많지 않다.
이 글에서는 닛산자동차의 전동 파워트레인 발전을 사례로 BEV와 e-POWER 모두를 다루어 보고, 특히 양산차에 채용된 전동 파워트레인의 제어에 대해 설명한다.
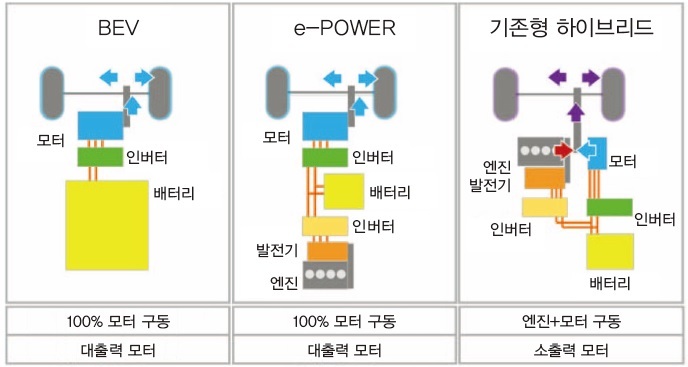
전동 파워트레인의 개요와 라인업
BEV, e-POWER, 그리고 하이브리드 전기자동차(Hybrid Electric Vehicle: HEV)의 구동 시스템 구성을 그림 1에 나타냈다. e-POWER는 시리즈 하이브리드로서 분류되는 하이브리드 형식으로, 높은 가속 성능과 액셀 조작성을 BEV의 개발로 얻은 전동 파워트레인의 제어를 통해 실현하는 동시에 발전 제어에 의해 엔진의 발전 소음이 잘 느껴지지 않는 특징이 있는 등 기존 시리즈 하이브리드와 차별화된다. BEV와 e-POWER 모두 100% 모터 구동 시스템으로, 구동륜은 모터의 출력이 감속기를 통해 접속된다. BEV와 e-POWER의 구동 모터·인버터를 공용함으로써 효율적으로 개발을 추진해 설비 투자와 비용 절감이 가능하다. 100% 모터 구동이라는 것은 모터의 고정도·고응답 제어의 장점을 BEV와 e-POWER에서도 얻을 수 있어 차량의 빠르고 부드러운 가감속을 실현하고 있다.
또한 e-POWER에서는 발전 전용 엔진이 타이어와 접속되어 있지 않기 때문에 엔진의 최량 연비 동작점을 집중적으로 이용함으로써 연비를 향상시킬 수 있을 뿐만 아니라, 엔진에 의한 발전 타이밍을 선택할 수 있는 자유도도 높다. e-POWER의 발전 제어에서는 로드 노이즈가 커지는 차속 조건이나 노면 거칠기 추정을 통해 엔진에 의한 발전 제어를 함으로써 BEV와 같은 정숙성을 실현하고 있다.
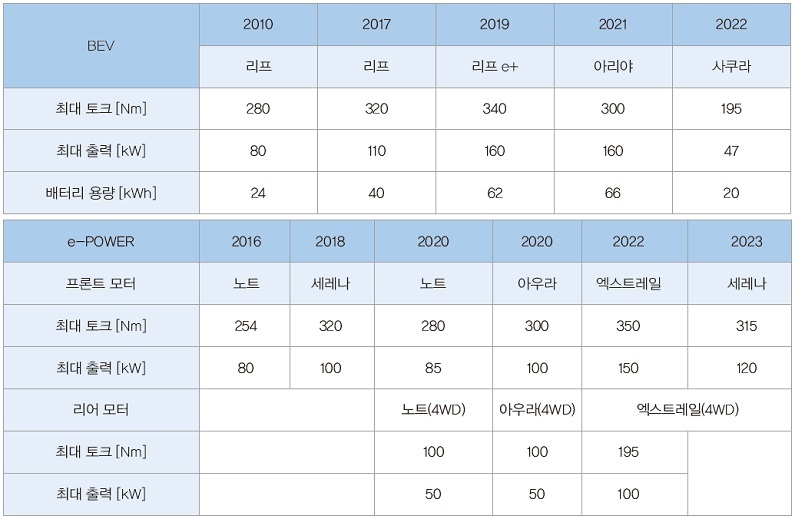
표 1은 BEV와 e-POWER의 라인업을 나타내고 있다. BEV는 닛산 리프의 모델 체인지와 함께 배터리 용량의 향상, 모터·인버터의 성능 향상을 실현하고, 닛산 리프를 통해 얻은 지견·경험을 바탕으로 새로운 플랫폼을 가진 SUV(Sport Utility Vehicle) BEV로서 닛산 아리야 또한 경차 BEV로서 닛산 사쿠라로 발전시켰다. 이들 전동 파워트레인은 배터리, 모터·인버터, 충전기를 각각의 차량 성능·사양에 적합한 부품을 탑재하고, 전동 파워트레인 제어는 공용시키면서 개량·발전시켜 각각의 차량에 맞게 제어를 적용하고 있다.
닛산 리프와 닛산 아리야 모터의 외관을 살펴보자 [참고문헌 1 참조]. 닛산 리프는 고효율 및 고토크·출력을 갖춘 매립 자석형 동기 모터(Interior Permanent Magnet Synchronous Motor: IPMSM)를 구동 모터로 채용, 스테이터 권선과 로터의 자석 배치 등을 개선해 모터의 코어 지름은 동일하게 하면서 축 길이를 바꿈으로써 e-POWER도 포함한 다양한 라인업에 대응하고 있다. 닛산 노트는 제1세대에서 제2세대로 진화하는 가운데 구동 모터를 85kW, 280Nm로 향상시키면서 모터의 축 길이 18% 감소, 기전 일체의 전동 파워트레인 유닛으로 사이즈 15% 감소를 실현했다.
닛산 아리야에는 새로 개발한 권선계 여자 동기 모터(External Excited Synchronous Motor: EESM)를 채용했다. 로터의 여자 전류를 제어함으로써 저토크 영역의 전자 가진력을 줄일 수 있고, 완가속이나 순행 등 구동력 요구가 크지 않은 경우의 정숙성을 향상시켰다. 또한 중희토류 원소의 비용·공급 위험을 줄일 수 있는 것이 특징이다.
전동 파워트레인의 제어
1. 전동 파워트레인의 시스템 구성
BEV와 e-POWER의 전동 파워트레인 제어 시스템 구성도를 각각 그림 2에 나타냈다. 이들의 중심이 되는 컨트롤러가 VCM(Vehicle Control Module)이며, 예를 들어 차량의 가속 페달이나 차량 속도, 배터리 충전 상태(State of Charge: SOC) 등을 바탕으로 구동력을 제어하고 인버터에 탑재되는 MC(Motor Controller)에 CAN(Control Area Network)를 이용해 모터의 토크 지령값을 송신한다. 이 전동 파워트레인의 부품군과 VCM은 EV-CAN이라는 네트워크를 구성하고, VCM은 차량 측의 ECU(Electric Control Unit)이 접속되는 V-CAN와 EV-CAN 간의 정보 게이트웨이로서 역할도 한다.
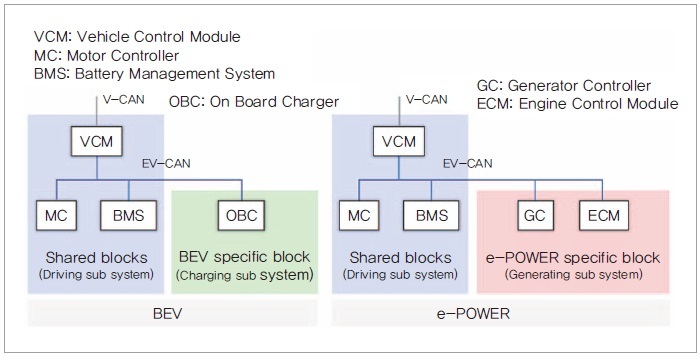
그림 2에 나타낸 Driving sub system의 BEV와 e-POWER의 구동력 제어는 전동 파워트레인의 ECU인 VCM과 MC 그리고 BMS(Battery Management System)에 의해 구성되고, BEV와 e-POWER가 모두 100% 모터 구동이기 때문에 이들 제어를 공통화할 수 있다. BEV의 충전 제어와 e-POWER의 발전 제어는 각각의 애플리케이션으로 제어 개발을 해서 전동식 파워트레인의 종류에 따라 선택하고 있다.
공통화된 구동력 제어에 대해서 이하에 설명하면, MC는 토크 지령에 기초해 검출한 모터 전류로부터 인버터의 각 반도체 스위치의 On/Off를 조작함으로써 모터 토크를 실현한다. MC는 인버터 캐리어 주파수의 고속 피드백 제어가 가능하며, 이 고속 제어의 특징을 살려 구동축 비틀림 진동 억제나 백래시 진동 억제 등의 모터 토크 제어가 실현되고 있다.
한편 VCM에서는 빠르고 부드러운 가감속 제어를 실현하는 토크 지령값을 생성하고, 브레이크와 모터 토크의 협조 제어를 실현하는 각각의 지령값 생성이나, 순행 시의 손실을 줄이는 제어 등의 기능을 가지며 구동력의 제어 중에서도 VCM·MC의 특징을 살려 기능을 분담시키고 있다. 이들 구동력의 제어가 BEV와 e-POWER에서 공용됨으로써 BEV에서 개발·발전한 기능은 e-POWER에 활용되고, 또한 e-POWER에서 개발된 기능을 BEV에 채용하는 것도 가능해 서로 진화·발전할 수 있다.
e-POWER 차량의 발진 시 가속 프로파일은 차량의 가속 성능으로서 중력 가속도에 대한 비율을 G로 나타내고 있다 [참고문헌 2 참조]. e-POWER 차량에서는 다른 HEV 차량과 비교해 0s의 가속 페달 밟기에 대해 높은 응답성을 나타내고, 또한 부드러운 가속을 실현하고 있다. 이것은 가속 페달 조작에 대해 지연이 적고 직선성 높으며 조작성이 좋은 차량이라는 것을 의미하므로 운전이 익숙하지 않은 운전자에게도 운전의 편의성이라는 가치를 제공한다.
2. 글라이딩 제어를 통한 순행 시 효율 개선
중고속 지역에서 순행하는 경우, 운전자가 미세한 액셀 조작에 의해 불필요한 가감속을 함으로써 모터 효율이 낮은 영역에서 역행·회생이 반복되어 모터 손실을 증가시키게 된다. 이 과제에 대해 차속에 따른 순행에 필요한 구동력 부근에서는 운전자의 미세한 액셀 조작을 취소해 모터의 손실을 줄이는 글라이딩 제어가 BEV와 e-POWER에 채용되고 있다 [참고문헌 3과 4 참조]. 글라이딩 제어에 의해 닛산 리프에서는 실용 항속 거리를 약 6% 향상시켰다.
3. 전동 AWD ‘e-4ORCE’에 의한 구동력 제어
전후륜 독립 모터 구동에 의한 전동 4WD(사륜 구동)은 e-POWER의 닛산 노트에 채용되어 전후 구동력을 제어함으로써 차량의 피칭 제어를 실현하고 있다. 또한 전륜과 후륜의 모터를 회생 제동할 때에 그 제동력 차이를 제어함으로써 회생 제동 시의 차체 자세 변화를 억제해 편안하고 부드러운 승차감을 제공할 수 있다. 이 전동 4WD를 발전시켜 모터에 의한 구동·회생에 더해 각 바퀴의 유압 브레이크도 조합한 제어로서 전동 AWD(All Wheel Drive) 제어인 ‘e-4ORCE(포스)’를 개발, ‘e-4ORCE’는 BEV의 닛산 아리야, 그리고 e-POWER의 SUV인 엑스 트레일에 채용되고 있다.
‘e-4ORCE’에서는 바퀴 하중의 변화에 의한 타이어 그립력의 한계 내에서 타이어 그립 능력이 최적이 되도록 구동력을 전후륜에 배분해 차량의 코너링 성능을 높이고 다양한 노면 상황에서도 높은 안정성을 실현하고 있다.
4. 구동 모터 제어를 이용한 축 비틀림 진동 억제
닛산 전동 파워트레인의 특징 중 하나인 빠르고 부드러운 가속 응답을 실현하는 제어의 핵심 기술로서 구동 모터 제어에 의한 축 비틀림 진동 억제를 들 수 있다. 초대 닛산리프의 개발 전부터 모터 제어 기술로서 개발이 진행되어 채용 후에도 진화·개량이 계속되고 있다. 구동 모터 토크 지령을 스텝으로 부여한 경우의 축 비틀림 진동 억제 효과를 보게 되면 [참고문헌 5 참조], 모터의 출력축과 타이어 사이의 드라이브 샤프트의 비틀림 강성으로 인해 모터 토크에 대한 모터 각속도의 응답은 약 8~10Hz로 현저한 공진 특성을 가진다. 완만하게 모터 토크를 변화시키면 비틀림 진동을 억제할 수 있지만 가속 응답을 저하시키게 된다. 이 트레이드오프 과제에 대해 그림 3에 나타낸 축 비틀림 진동 억제에서는 구동 토크의 전달계와 차량 운동을 모델화해 공진 특성이 없는 규범 응답과 전달 특성의 역계로부터 피드포워드 보상기를 설계하고 로버스트성을 높이기 위해 피드백 보상기를 병용하고 있다.
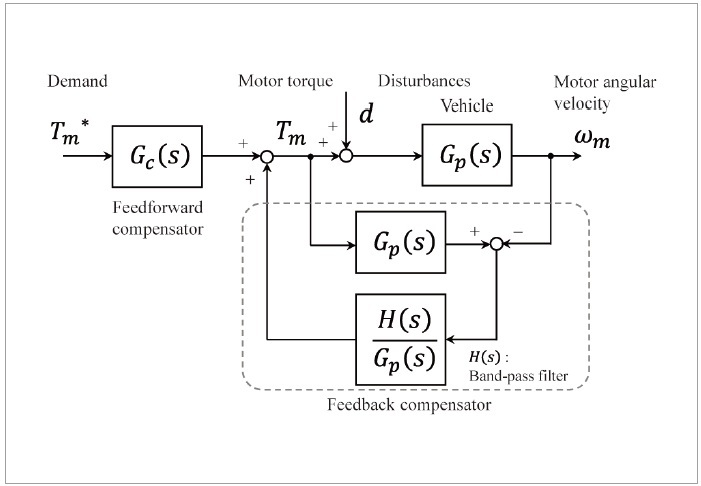
이 축 비틀림 진동 억제를 바탕으로 닛산 리프에서 ‘e-Pedal’을 채용할 때에 구동 모터의 회생 및 역행 전환 시의 기어 백래시 특성도 고려한 제어로 발전시켰다 [참고문헌 6 참조]. ‘e-Pedal’은 가속 페달 조작만으로 발진·가속·감속·정지를 할 수 있는 기능으로, 가속 페달과 브레이크 페달의 전환 조작을 줄임으로써 운전 조작의 부하를 저감할 수 있으며 진화된 ‘e-Pedal Step’이 닛산 아리야와 e-POWER 차량에 채용되어 있다.
맺음말
BEV와 e-POWER의 전동 파워트레인은 구동 시스템을 공용할 수 있으며, 양쪽의 진화를 상호 채용하는 것이 가능하다. 구동 모터·인버터의 공용뿐만 아니라, 전동 파워트레인의 제어는 구동력 제어·모터 제어의 계층 각각을 공용화함으로써 100% 모터 구동의 매력과 가치를 널리 제공하는 데 기여하고 있다.
[참고 문헌]
(1) 大久保, 和田:ARIYA의 성능을 실현하는 신개발 모터,日産技報,No.88, 69/72 (2022)
(2) 木村, 風間, 河合, 向, 關, 衛藤:차세대 하이브리드 파워트레인 “e-POWER” 개발,日産技報,No.80, 6/14 (2017)
(3) 關, 吉本, 黒澤, 島村:신형 전기 자동차의 전동 파워 트레인, 자동차 기술회 학술 강연회 예고집(가을),1475/1480 (2017)
(4) 關, 黒澤, 吉本, 島村:신형 닛산 리프의 전동 파워 트레인 제어 시스템,日産技報,No.82, 16/22 (2018)
(5)小野山,吉本:닛산 전기 자동차 용 파워 트레인의 진화,日産技報,No.82, 3/7 (2018)
(6) 大野, 澤田, 小松, 藤原, 中島:모터 제어에 의한 백래시 진동 억제,日産技報,No.82, 23/29 (2018)
요시모토 칸타로, 도쿄전기대학 미래과학부 로봇․메카트로닉스학과
하뉴 토모유키, 닛산자동차주식회사