미래의 배터리 생산 요구사항을 충족하도록 특별히 설계된 차세대 센서 개발
2022년에는 1,200만 대 이상의 전기차가 판매되었으며, 이는 2021년에 판매된 것보다 65% 더 많은 수치다. 수요 증가는 이미 자동차 제조 환경을 영구적으로 변화시켰으며 거의 모든 주요 자동차 회사가 현재 전기차 생산 라인을 운영하고 있다.
전기차는 내연기관 차량보다 움직이는 부품이 적지만 제조는 여전히 매우 복잡하다. 고정자 및 회전자에서 복잡한 배선 하네스에 이르기까지, LMI는 많은 전기차 제조 응용 분야와 관련되어 있다. 그러나 전기차의 핵심은 배터리이며, 여기에서 머신비전 솔루션이 시장 성공에 필수적이 되었다.
전기차 배터리 제조 개요
전기차 배터리 제조는 (1) 전극 제조, (2) 셀 조립 및 패키징, (3) 셀-모듈 조립, (4) 모듈-팩 조립, (5) 최종 설치 검사 등의 5가지 일반 단계로 나눌 수 있다.
Gocator 3D 스마트 센서와 내장형 온-보드 측정 툴은 이 제조 공정의 모든 단계에서 사용된다. 이러한 응용 프로그램을 개별적으로 간단히 살펴보겠다.
전극 제조: 이 단계에서 Gocator 센서는 슬러리가 적용될 때 전극의 균일한 모양과 두께를 보장하는 데 사용된다. 센서는 셀 시트의 탭 사이의 거리를 측정하는 데에도 사용된다. 이러한 응용 분야에서는 공차가 매우 작기 때문에 고해상도 및 작은 FOV의 센서가 사용된다.
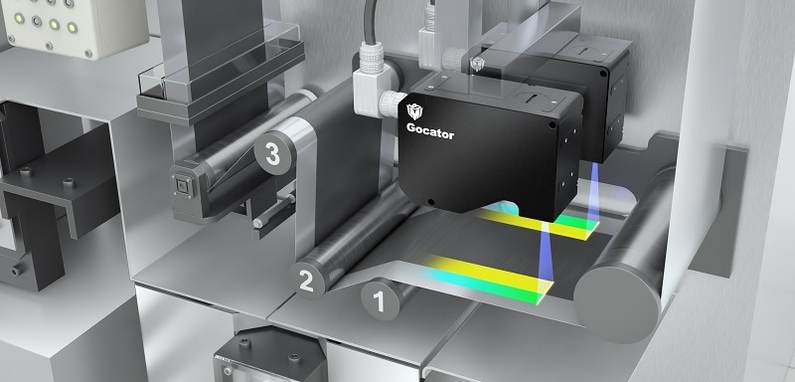
셀 조립 및 패키징: 전기차에 사용되는 셀 유형은 일반적으로 원통형, 각형 그리고 파우치형이다. 원통형 셀은 그룹으로 함께 포장되어 존재/부재, 올바른 위치 및 치수, 셀 상단의 찌그러짐이나 긁힘과 같은 잠재적인 표면 결함에 대해 스캔된다.
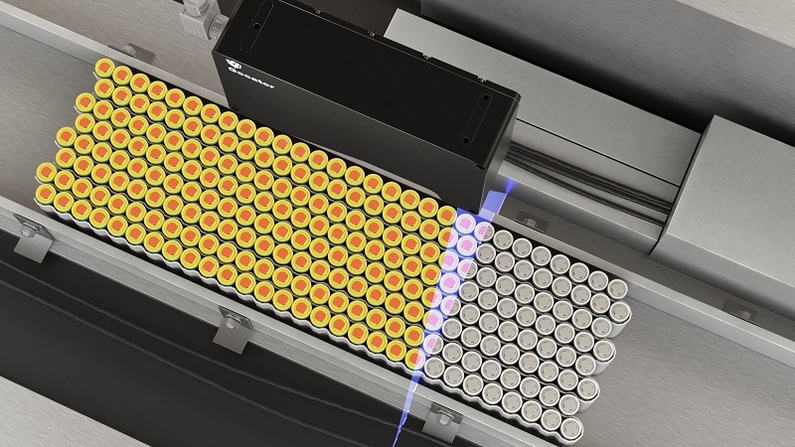
용접 전에 Gocator® 또는 멀티센서 네트워크는 고속 3D 레이저 프로파일링 및 각형 배터리 셀과 금속 케이스 사이의 갭-단차를 측정할 수 있는 내장 툴을 제공한다. 용접 후에는 용접 솔기가 균일하고 공차 내에 있는지 다시 검사한다.
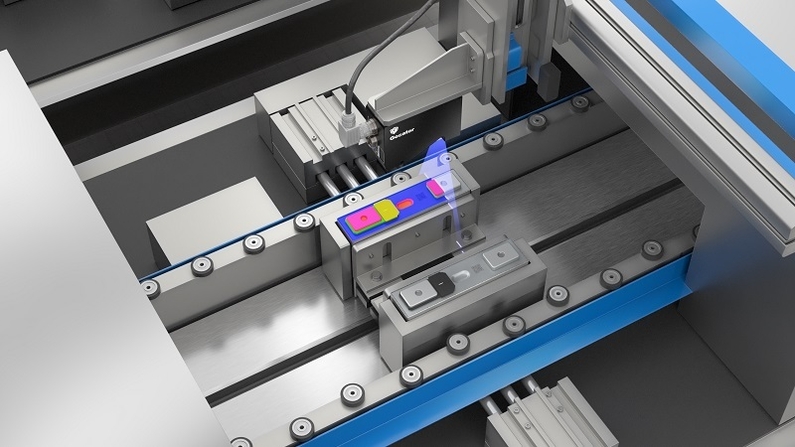
배터리 셀 표면의 정확한 치수를 검사하고 표면, 가장자리 및 모서리의 결함을 감지해야 한다.
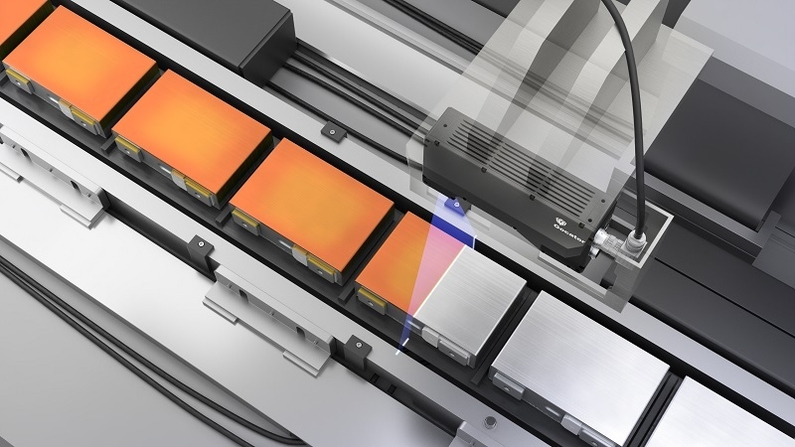
셀-모듈 조립: 개별 배터리 셀이 품질 관리를 위해 검사되면 정해진 수의 배터리 셀이 정확하게 그룹화되어 배터리 모듈을 형성한다. 예제 애플리케이션은 센서가 각 모듈의 용접 이음새(주로 버스바 검사)를 측정하고 검사하는 것이다.
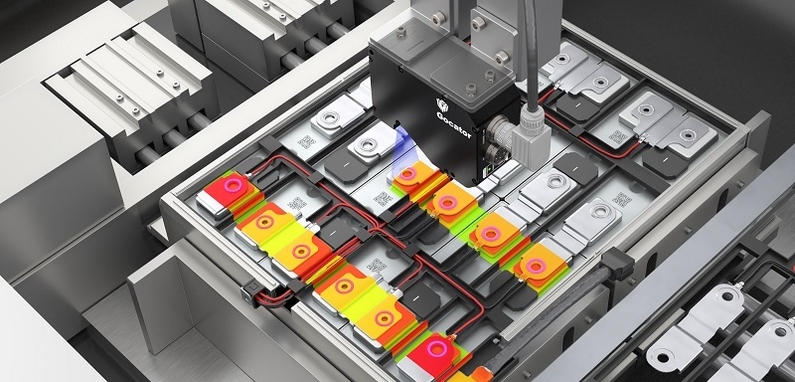
최종 설치 검사: 전기 자동차의 경우 대형 트레이/팬이 바닥 패널 아래에 있다. 리튬 이온 배터리 팩은 이 트레이에 접착되어 있다. Gocator 센서는 이 최종 단계에서 올바른 치수(높이, 부피, 너비, 길이) 및 표면 품질(깨짐, 틈, 넘침 등)에 대해 글루 비드 적용을 검사하는 데 사용된다.
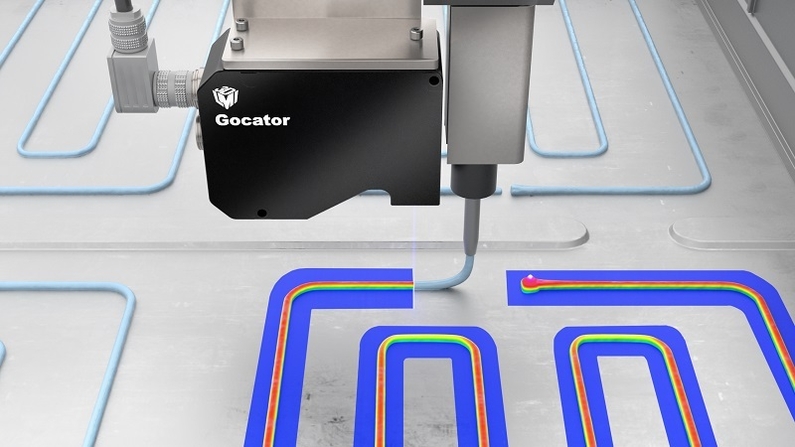
마무리
전기차 배터리 생산은 전 세계적으로 빠르게 성장하고 있다. LMI는 현재 산업을 지원할 뿐만 아니라 미래의 배터리 생산 요구사항을 충족하도록 특별히 설계된 차세대 센서를 적극적으로 개발하고 있다.
LMI Technologies ㅣ
헬로티 김진희 기자 |