칸토 켄타, DMG모리세이키 계측개발부 부장
하나하나의 개별적인 요구에 대응하는 ‘다품종 소량 생산’에서 그 형상을 정확하게 만들어내는 요구가 증가하고 있으며, 현재는 대부분의 복잡한 형상을 가진 기계가공 부품이 5축가공기로 제조되고 있다.
예를 들면 터빈 블레이드나 대형 기어와 같은 치수의 평가뿐만 아니라 형상이 중요시되는 워크가 5축가공기에서 날마다 만들어지고 있는데, 이들 워크는 그 정도에도 엄격한 값이 요구되고 있다. 또한, 재가공을 할 필요가 있는 경우, 한번 떼어낸 워크를 다시 5축가공기에 설치하는 위치 재현성에 대해서도 엄격한 값이 요구된다. 이러한 경우에는 워크를 가공기에서 떼어내어 기기 외부에서 측정하는 것이 아니라, 기기 내에서 가공한 그대로의 상태로 직접 측정을 하는 ‘원척 대응’이 가공의 효율화에 효과적이다.
현재 터치프로브를 이용한 기내 측정을 해서 재가공 전의 얼라이먼트나 워크 확인을 위한 측정이 널리 실천되고 있는데, 터치프로브 측정으로 인한 짧은 작동 거리, 접촉력 등의 문제가 있는 것도 사실이며, 또한 터치프로브 측정에서는 기본적으로 측정 요소는 ‘치수’가 되므로 그 복잡한 형상을 평가하는 것에는 충분하지 않다는 문제도 있었다.
이러한 문제를 해결하기 위해 비접촉 레이저 스캐닝 프로브를 사용하는 것은 잘 알려져 있지만, 이것은 측정기에서 하는 대응으로 생각되고 있었다. 고정도를 유지하기 위해서는 레이저 스캐닝 프로브 자체의 정도가 충분할 필요가 있고 또한 프로브의 장착 자세 보정 등도 필요한데, DMG모리세이키에서는 이러한 과제를 해결해 공작기계 상에서 레이저 스캐닝 프로브의 형상 계측을 실현하는 시스템을 개발했다(그림 1).
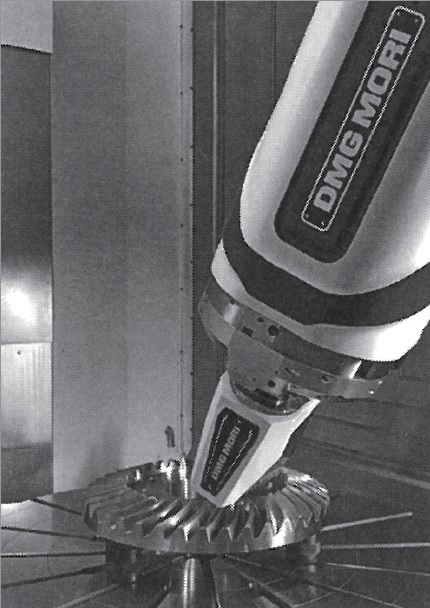
복합화 : 공작기계와 계측
수십 초에 하나의 부품을 만들어내는 양산 라인에서 공작기계상의 계측을 실천하는 것은 생산성을 떨어트리는 것으로 생각된다. 그러나 앞에서 말했듯이 다품종 소량 생산과 같은 워크에서는 그 부가가치나 부품 단가가 높고, 또한 가공의 실패가 허용되지 않는 것도 있어 기상 계측을 함으로써 토털 스루풋을 높이고 제품 단가를 억제하는 것이 생각된다. 또한, 대형 워크의 경우, 워크 자체의 이동 등에 위험을 동반하기도 해 고정도가 요구되는 워크의 경우는 재가공을 위한 위치 분할에 긴 시간을 소비하기도 한다.
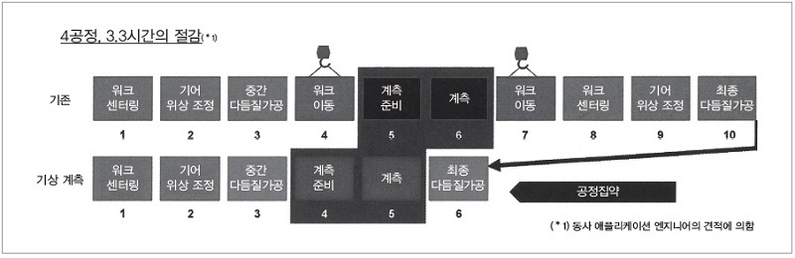
그림 2는 대형 기어를 5축가공기로 가공한 경우의 프로세스에서, 기존대로 기기 외부의 측정기로 측정을 한 경우와 기기 내에서 측정을 한 경우의 비교이다. 워크를 측정기로 이동시키기 위한 시간이나 워크 재설치의 시간 등을 기기 내 계측에서는 생략할 수 있고, 10프로세스였던 것이 6프로세스로 단축되어 4공정, 3.3시간의 절감 효과가 있다고 생각된다. 또한, 이동에 동반되는 위험이나 재가공 전의 위치 분할 오차에 의한 가공 불량 가능성도 배제할 수 있다는 장점이 있다.
터치프로브와 레이저 스캐닝 프로브
터치프로브의 측정은 접촉자를 워크에 대고 그 좌표 위치를 구해, 그들 여러 개의 데이터로부터 치수를 계산하고 있다. 실제로 워크와 접촉하기 때문에 미세한 정도의 흠집을 내기도 하고, 얇은 워크는 그 압력에 의해 변형이 생길 가능성도 있다.
또한, 터치프로브의 측정은 접촉점의 법선 방향으로 스타일러스 보정을 하고 있어, 워크의 소성을 알고 있는 상태가 아니면 정확한 방향으로 보정할 수 없기 때문에 미지의 워크 측정은 힘들다.
한편, 레이저 스캐닝 프로브를 이용한 측정에서는 비접촉으로 데이터를 취득하기 때문에 워크를 손상시킬 위험이 없다. 또한, 측정 범위가 매우 넓고, 형상 불명의 워크 측정에도 간단히 적용할 수 있어 고밀도의 데이터를 취득할 수 있다. 레이저 스캐닝 프로브에 의한 고속 스캔은 복잡한 형상이나 자유곡면에 적합하다고 할 수 있다.
데이터 취득 속도와 정도의 균형이 잡힌 레이저 스캐닝 프로브의 측정 원리로서 일반적으로 광절단 방식이 알려져 있다. 이것은 측정 부위에 빛을 비춰 그 확산광을 검출함으로써 측정 부위의 높이 정보를 얻는 것이다. 일괄적으로 광범위 형상을 취득하는 것을 주로 하고 있으며, 자유곡면 평가에 적합하다고 할 수 있다. 단, 앞에서 말한 측정 원리 때문에 빛이 도달하지 않는 깊은 홈이나 구멍의 바닥 측정이나 빛이 투과해 버리는 투명한 부품의 측정 등에는 적합하지 않다. 터치프로브를 포함해 요구되는 측정에 따라 측정 기법을 바꾸는 것은 매우 중요하다.
기상 계측 시스템
DMG모리세이키에서는 다품종 소량 생산의 ‘고정도화’, ‘토털 스루룻 향상’을 실현하기 위해 5축가공기 DMU/DMC 시리즈에 탑재할 수 있는 기상 계측 시스템을 출시했다(그림 3).
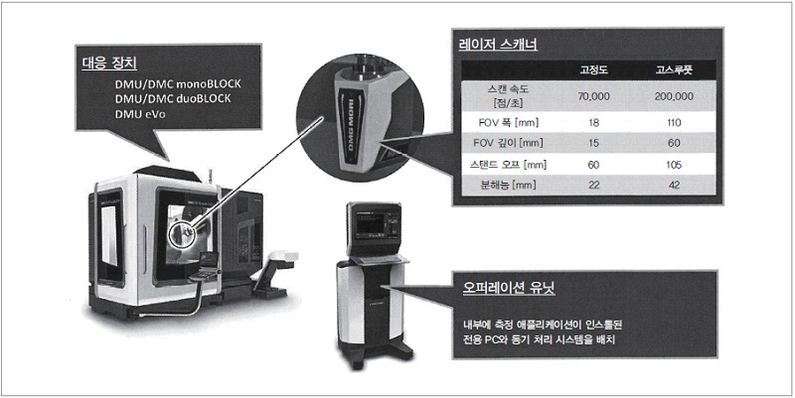
이 시스템은 5축가공기의 스핀들에 레이저 스캐닝 프로브를 장착, 구동축을 제어해 워크의 형상에 맞춘 스캐닝을 실현하고, 그 형상 데이터를 점군 데이터로서 받아들일 수 있도록 만들어졌다. 레이저 스캐닝 프로브는 기어나 금형 등의 측정에 적합한 고정도판과 넓은 범위를 일괄적으로 취득할 수 있는 고스루풋판의 2종류를 준비했다.
5축가공기의 좌표값 정보와 레이저 스캐닝 프로브의 계측 결과를 바탕으로, 점열의 데이터로서 생성하는 것이 오퍼레이션 유닛 내에 설치된 PC이다. 이 PC에는 5축가공기의 제어와 취득한 데이터를 처리하는 측정용 소프트웨어가 인스톨되어 있어 항상 조작은 모두 이 오퍼레이션 유닛 상에서 하게 되는데, 취득한 데이터를 차분히 해석하고 싶은 경우 등에는 물론 데이터를 이동시켜 오피스 환경에서 평가 작업을 할 수도 있다.
데이터를 고정도로 취득하는데 중요한 포인트의 하나로서 5축가공기의 각 축 좌표값과 레이저 스캐닝 프로브로 취득한 화상의 동기 처리를 들 수 있다. 이 시스템에서는 독자적으로 개발한 동기 처리 시스템을 이용해 좌표값과 화상의 동기 어긋남 오차가 1μm 이내가 되는데 성공, 측정 정도의 향상을 실현할 수 있었다.
또한, 측정 전에 테이블에 설치된 기준구를 측정해 주축에 장착된 레이저 스캐닝 프로브 자신의 미세한 장착 자세의 보정도 하고 있다. 그 외에 회전축 보정 등도 함께 함으로써 고정도의 데이터를 취득하는 것이 가능하다. 또한, 이들의 보정값 취득에 대해서는 미리 프로그램이 준비되어 있기 때문에 작업자를 번거롭게 하지 않고 측정 준비를 할 수 있다.
1. 측정 정도
이 시스템에서 실제로 테이블상에 구를 설치하고, 그 구심 위치와 구의 지름 및 구면도를 40회 반복 측정한 결과를 표 1에 나타냈다.

구심 위치에 대해서 X방향으로 0.37μm, Y방향으로 0.45μm, Z방향으로 0.84μm라는 매우 높은 반복 정도를 확인할 수 있다. 또한, 구 지름의 측정에서는 25mm의 구를 측정해 24.9982mm가 되고, 그 반복 정도는 1.0μm 이하로 이쪽도 또한 매우 높은 반복 정도를 확인할 수 있다.
2. 대형 기어 측정
이 시스템의 최초 대상 워크로서 대형이기 때문에 이동이나 설치에 많은 시간이 필요하고, 높은 가공 정도를 요구받는 대형 기어를 설정했다. 기존 기어는 전용기의 가공이 주류였는데, 최근 5축가공기의 정도 향상과 전용기에 대한 설비 투자 금액이 크기 때문에 대형 기어의 가공을 5축가공기로 실현하는 경우가 많아지고 있다. 기어의 치면 평가에서는 높은 정도를 요구받으므로 동사의 기상 계측 시스템의 최초 목표물에 적합하다고 생각했다.
또한, 5축가공기를 사용한 기어가공에서는 보통의 치형 형상을 가진 기어뿐만 아니라, 특수 치형을 가진 기어의 가공도 가능하며, 암텍(Amtec)과 응용과학연구소가 고려한 IP 베벨 기어(Invo Planar bevel gear)와 같은 전용기가 가진 제약에 구애받지 않는 자유로운 치면 설계를 할 수 있게 된다. 이와 같은 기어의 치면 형상을 평가하는데 있어, 치면 전체의 형상을 점군으로 받아들일 수 있는 동 기상 계측 시스템은 매우 효과적이다.
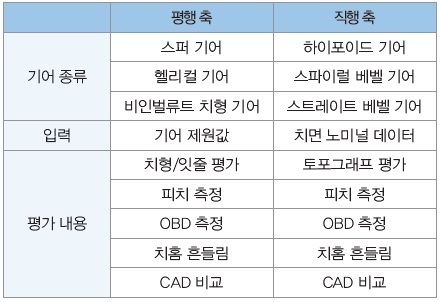
이 시스템에서는 표 2와 같은 대상 기어와 평가가 가능하며, 실제 치면 형상 데이터로서 그림 4와 같은 점군 데이터를 취득할 수 있다. 이 형상 데이터를 사용해 치형, 잇줄, 피치 오차 평가 등 일반적으로 기어 평가에서 실시되는 항목을 모두 평가할 수 있다(그림 5).

접촉식 3차원 측정기의 측정 결과와 이 시스템의 측정 결과의 비교를 그림 6에 나타냈다. 치형, 잇줄의 윤곽 형상은 동등한 것이 출력되고 있으며, 또한 이들의 윤곽선에서 산출된 기어의 평가 지표도 대략 2μm의 폭에 들어간다. 더구나 그들 값에 대해서 40회 측정한 반복값을 확인한 결과, 2μm(2σ) 이하였다.
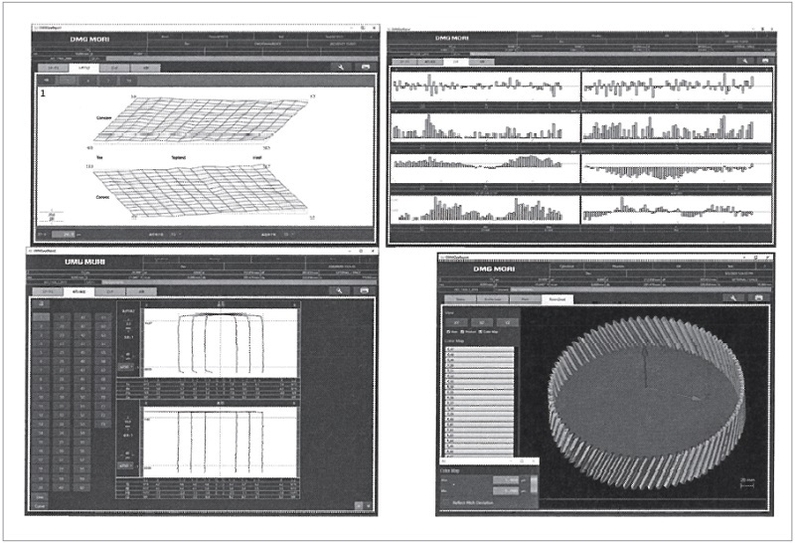
또한, 이 시스템에서는 치면 모델과 형상 비교도 할 수 있고, 형상 데이터가 가진 가능성을 충분히 살릴 수 있다. 미래적으로는 이 형상 데이터를 사용해 이맞음(Tooth contact)의 시뮬레이션을 하거나, 형상 오차 데이터로부터 자동으로 가공패스를 수정하는 기능 등에 대해서도 검토해 갈 생각이다.
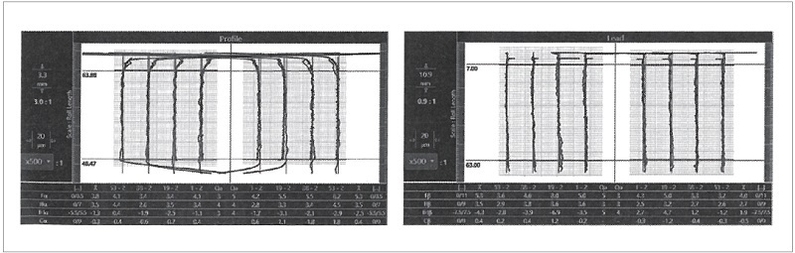
범용 워크 측정
이 시스템은 범용의 비접촉 기상 계측 시스템으로, 기어 이외의 형상 계측도 당연히 가능하다. 기존에는 평가가 어려웠던 자유곡면 형상을 가진 워크, 예를 들면 터빈블레이드와 같은 부품에 대해서도 이 시스템에서는 자유롭게 평가를 할 수 있다.
형상 계측 시스템의 장점 중 하나는 그 데이터를 보존할 수 있어 나중에 여러 가지 평가가 가능하다는 점이다. 그림 7은 취득한 블레이드의 형상 데이터이고, 그림 8은 형상 데이터와 CAD 모델을 비교한 것이다.
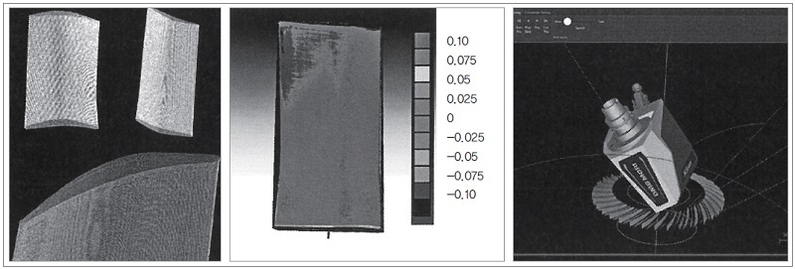
그리고 형상 데이터를 XY 평면에 수평으로 절단한 윤곽 형상 데이터를 생성하는 것도 가능하고, 이 데이터를 사용해 블레이드의 두께나 폭 등을 2차원적으로 평가하는 것도 가능하며, 또한 끝단 부분의 윤곽 형상 데이터를 사용해 블레이드 에지부의 R을 계산하는 것도 가능하다. 이들은 데이터로서 보존이 가능하기 때문에 가공이 끝나고 실물의 워크가 출하되어도 그 워크 데이터는 항상 남길 수 있어 어떤 문제가 발생했을 때에는 그 데이터를 다시 확인함으로써 트레이서빌리티의 확보라는 점에서도 큰 장점이 있다고 생각된다. 또한, 도면이 없는 보수 부품의 리버스 엔지니어링에 적용하는 것도 유용하다.
소프트웨어
취득한 점군 데이터에 대해서는 범용의 점군 처리 측정 소프트웨어를 준비하고 있으며, 그쪽에서 여러 가지 측정 연산을 할 수 있게 되어 있다.
보통의 3차원 측정기의 측정과 마찬가지로 취득한 데이터로 좌표계를 설정하거나 측정 요소를 조합한 측정, 그리고 이들과 같은 기존의 치수 측정을 하는 것뿐만 아니라, 받아들인 점군 데이터를 사용한 기하공차 판정도 가능하다. 또한, 기어에 대해서는 전용의 기어 평가 소프트웨어를 준비하고 있어, 범용 소프트웨어와 연동해 데이터 취득에서 평가까지 심리스하게 실현하는 환경을 제공하고 있다.
또한, 점군을 취득하는데 있어 스캐닝 패스(어떻게 스캔을 할지)를 시스템에 학습시킬 필요가 있는데, 이번 기어의 측정에서는 모델을 입력함으로써 거의 자동적으로 그 최적의 스캐닝 패스를 생성하는 기능을 개발했다(그림 9).
현 단계에서는 대상은 기어뿐이지만, 앞으로 일반 3D 모델을 베이스로 최적의 스캐닝 패스를 생성하는 기능을 개발해 갈 것이다.
맺음말
지금까지 설명했듯이, 이 기상 계측 시스템을 사용해 5축가공기의 가공에서 공정 절감, 복합화를 실현할 수 있고, 원척의 프로세스 실현 및 고정도의 형상 평가를 할 수 있다.
다품종 소량 생산 환경에서 안정적으로 고정도 가공을 하고, 효율적으로 양품을 출력하는 프로세스 실현에서 이 시스템이 그 한 부분을 담당할 것으로 생각한다.
또한, 현 시점에서는 ‘형상 평가’에 머물러 있지만, 미래적으로 형상 평가 결과인 형상 편차 데이터와 가공에 부수되는 파라미터나 공구 상태 등을 인풋해서 최적의 가공패스를 아웃풋하는 피드백 루프를 구성할 수 있도록 앞으로 개발을 추진해 갈 것이다. 이 기능을 반드시 실현해 가공 공정의 효율화를 목표로 노력해 갈 것이다.